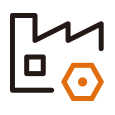
Easy "wrong material" because of a variety of materials
The increasingly high product design accuracy, increasingly smaller and varied components have made it difficult to differentiate the materials from the appearance, easily leading to mistakes in material issuing or feeding.
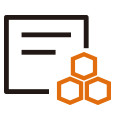
High inventory of raw materials and sluggish WIP
The low degree of integration of enterprise information system results in the lack of effective on-site data. In the market situation featuring little investment, short cycle and quick results, the enterprises are generally faced with such problems as untimely communication and serious lag in demand response, leading to a high raw material inventory level, an excessive warehouse area, and sluggish WIP in the production line.
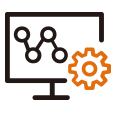
Low equipment utilization
Because of no real-time equipment connection, equipment performance in terms of OEE, capacity and quality first pass yield can’t be promptly analyzed, and production waste can’t be promptly identified, resulting in low utilization rate of equipment.
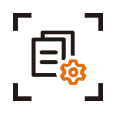
Low volume/high mix and frequent changeover
With the diversification of market demand, enterprise orders tend to be placed in "low volume/high mix" mode. Frequent changeovers, long changeover cycletime, low production efficiency, wrong material and other emergencies contribute to the high production cost of enterprises, and no guarantee in production quality.
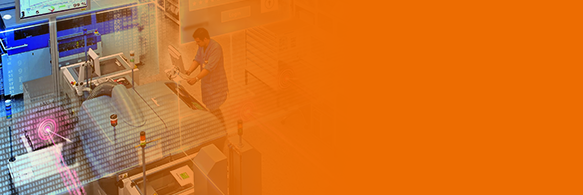
MES(Manufacturing Execution System)
By integrating the planning schedules and the material sequence list of each machine, the intelligent production changeover function is designed to help with off-line material binding and intelligent online material check in the production process, so as to achieve rapid changeover and no feeding error. The production information of each station can be collected and analyzed in time.
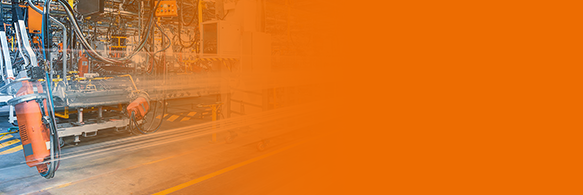
WMS(Warehouse Management System)
Through label printing, each material is given a unique ID. Through barcode scanning technology, comprehensive information scanning operation during material receiving, warehousing, drawing and issuing can be realized, effectively solve the wrong material problem in the traditional operation mode and achieve material FIFO management.
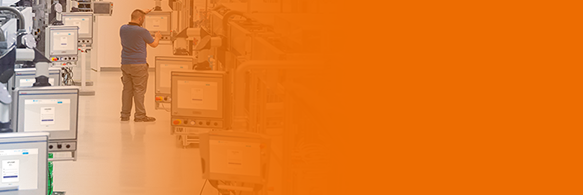
QMS(Quality Management System)
It focuses on helping 3C enterprises to establish a comprehensive man, machine, material and method, quality traceability system from original ERP materials to work order traceability, and avoid different quality anomalies such as mixed work orders, skipping stations and missing stations in the process through station barcode scanning control of each product.
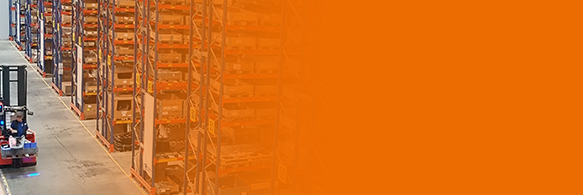
EAM(Enterprise Asset Management System)
It focuses on changing the traditional paper-based manual inspection and maintenance of equipment in 3C enterprises. Through EAM, operators can easily maintain the equipment through mobile phones, promptly collect and record relevant information of each piece of equipment, and call past experience for sharing.
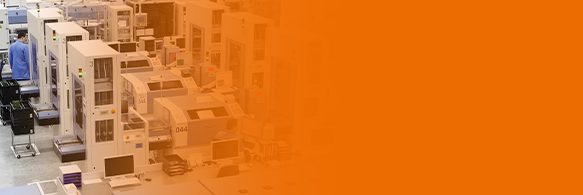
IoT(Internet of Terminals)
It focuses on solving the problem no communication of many equipment in 3C enterprises. By obtaining the data of each machine, it can realize effective utilization in production scenarios and management, and achieve the improvement of utilization rate of equipment and overall production efficiency.
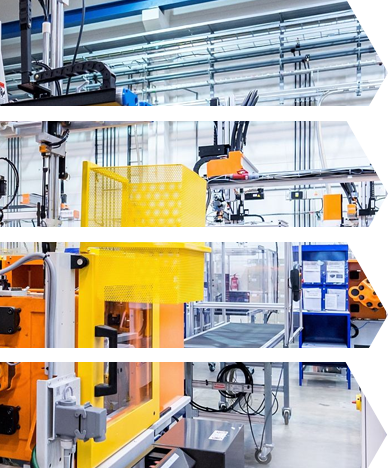
Warehousing information management
Through the unique ID of each material, fast recieving of warehousecan be achieved, and through the design of dynamic storage locations, the utilization rate of the warehouse can be improved by more than 20%; through connection with the MES, the use of JIT+ first set on-demand delivery mode can save manpower by more than 15%.
Production coordination, intelligent production switchover and fast changeover
Cancel the line side warehouse and adopt the distribution operation from the warehouse to the production line through the connection of WMS and MES; bind off-line materials in advance, obtain the material sequence list of the machine, and carry out intelligent changeover through the integration of planning and scheduling and equipment communication. The changeover time is reduced by 15 to 30 minutes each time.
Total quality management
Establish the comprehensive man, machine, material and method quality traceability system of all products, form accurate forward and backward traceability of each product to minimize the losses to and impact on the enterprise in case of quality problems.
Information managment system of enterprise asset
Realize the interconnection and interaction between various equipment within the enterprise, include assets and spare parts into the system for efficient general check, maintenance, requisitioning etc... information-based management. Further realize the closed-loop life cycletime management of each equipment from factory delivery to scrapping.
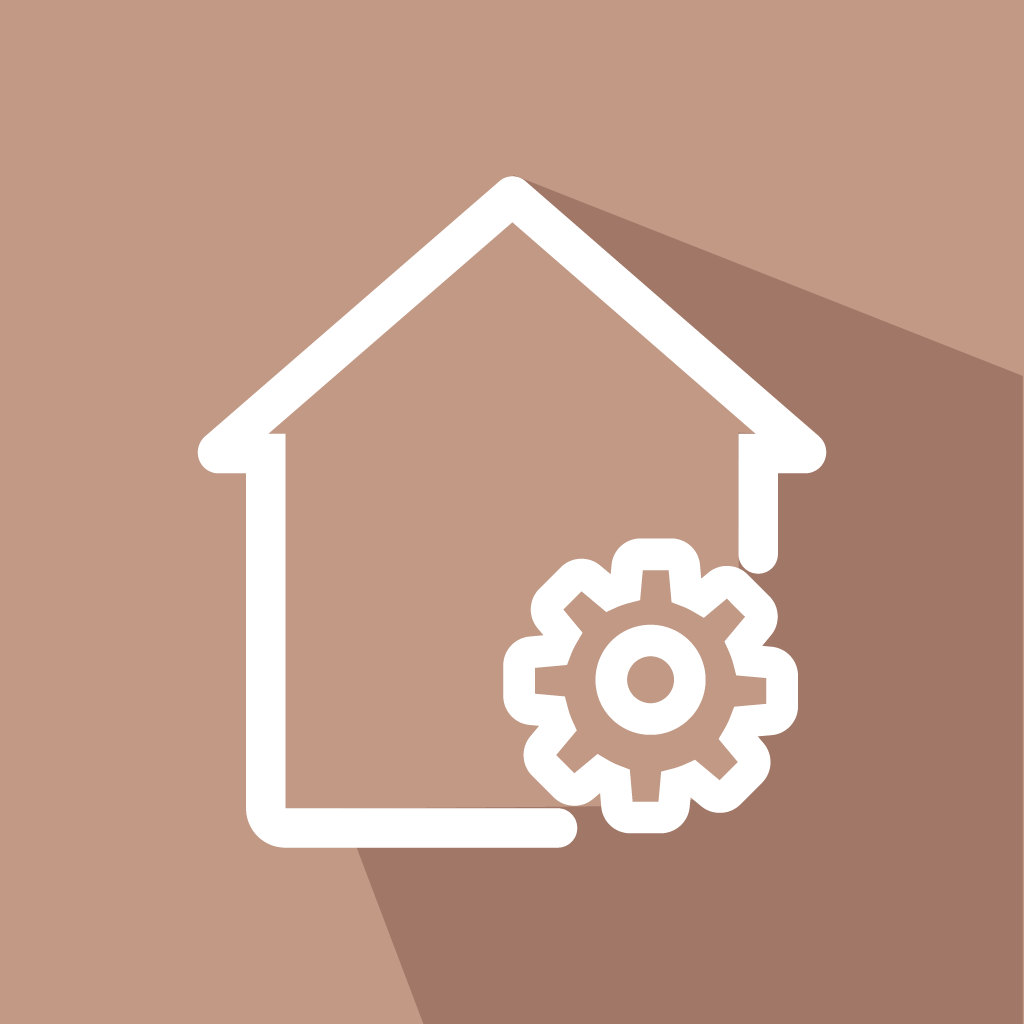
WMS
Warehouse Management System
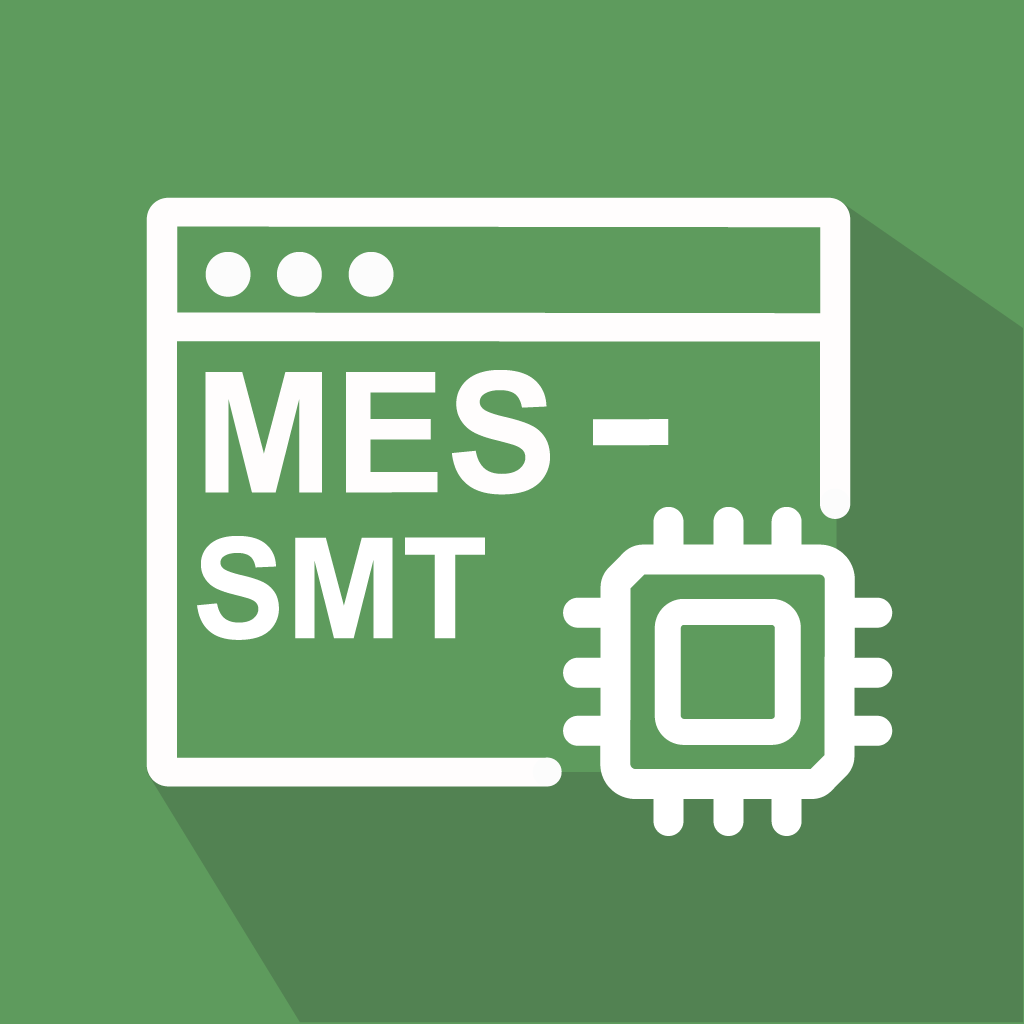
MES
Manufacturing Execution System
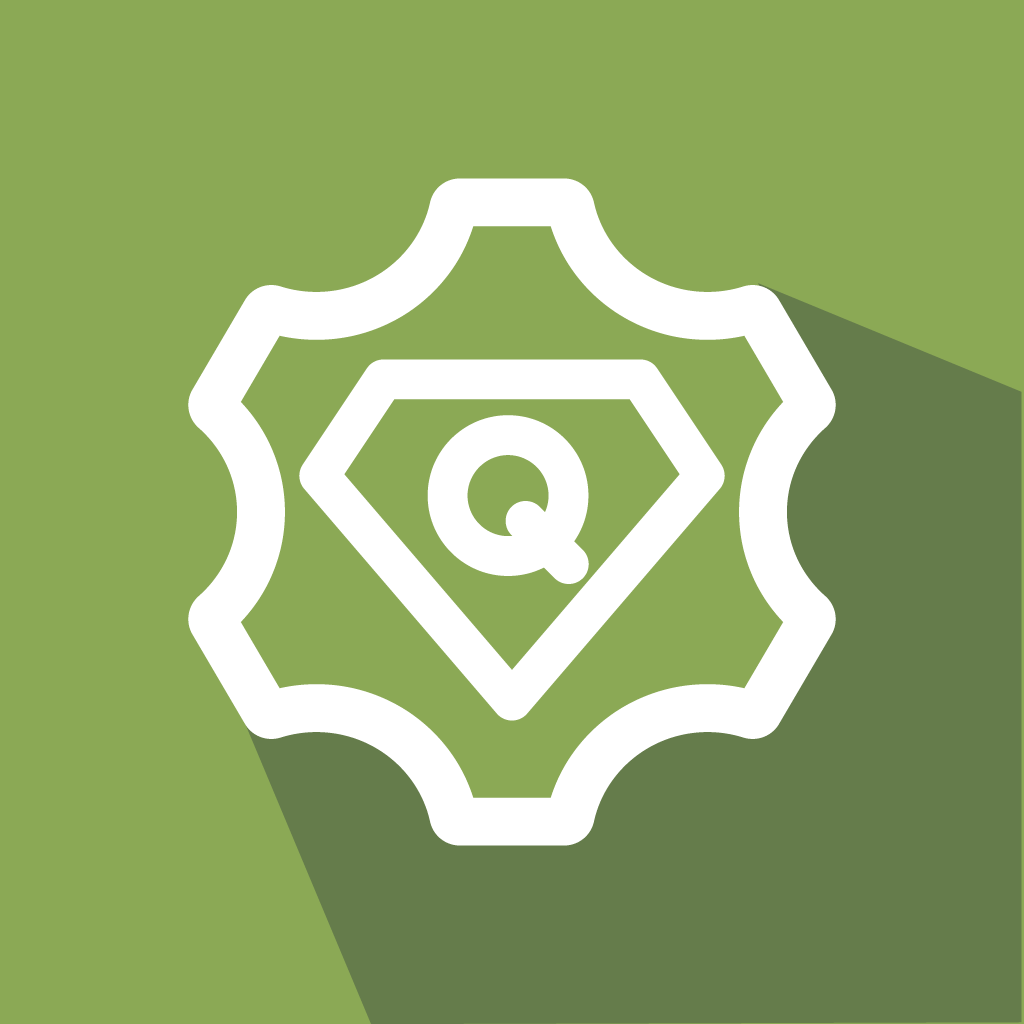
QMS
Quality Management System
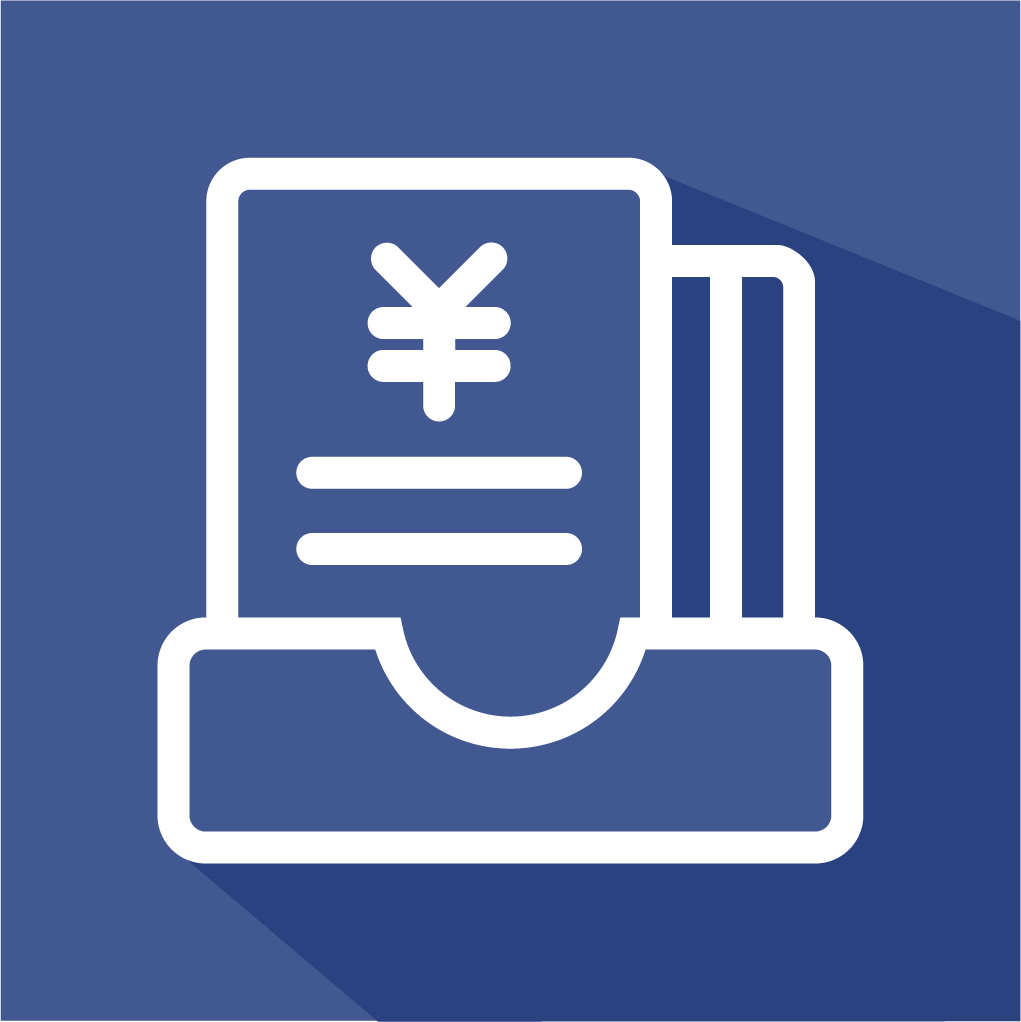
EAM
Enterprise Asset Management System
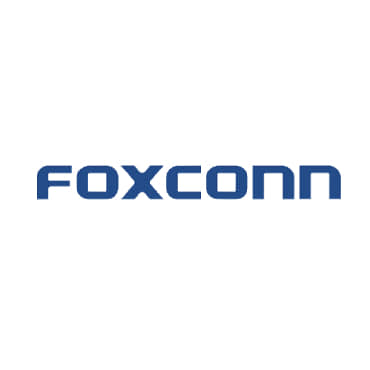
Foxconn Technology Group
Shenzhen, Guangdong
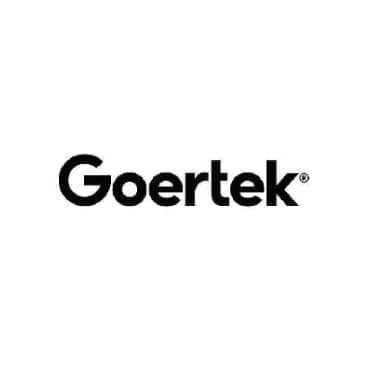
Goertek Inc.
Weifang, Shandong
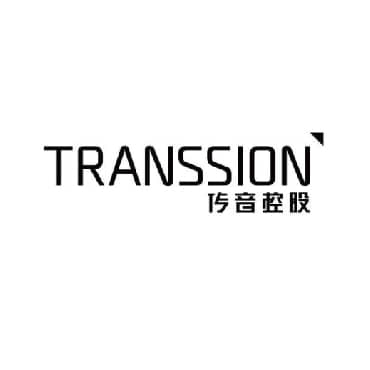
Shenzhen Transsion Holdings Co., Ltd
Shenzhen,Guangdong